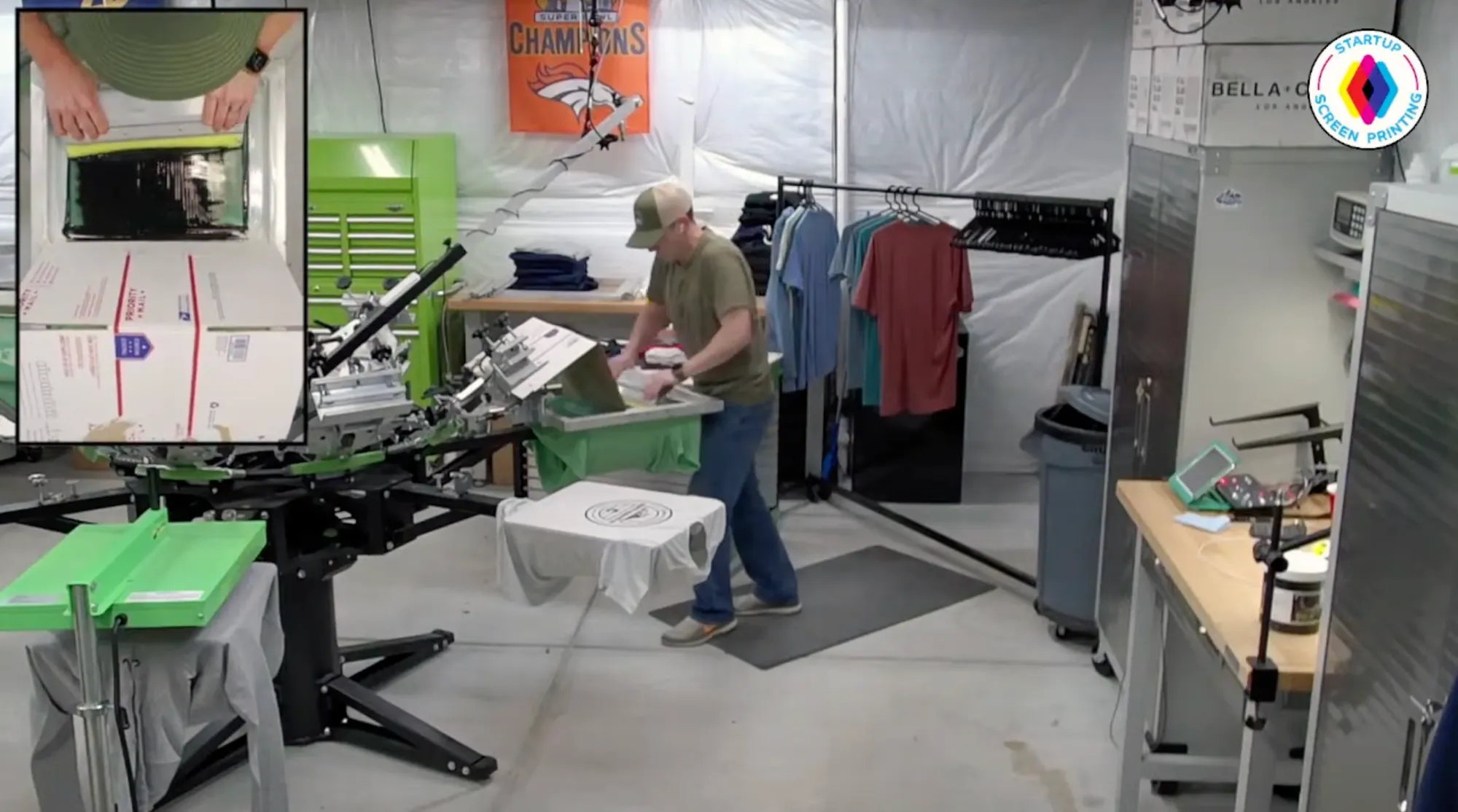
When I started my print company back in 2017, I was printing in a small 6x10 room in the basement of a rental house. I had to wash screens out in the yard. I had an exposure unit sitting on the counter in the bathroom and I was wash the screens in the bathtub after exposing. It was extremely tight and it wasn’t an ideal space for screen printing, but I made it work. Thankfully (although it was a pain at the time) we had to move a few months later. The new house we moved to (also still renting) had a large unfinished basement that was going to be perfect for a print shop. That was in mid-2017 and since then I’ve slowly upgraded the shop to where it is now. It’s not perfect, but I love it.
The press
Let’s get to the most exciting part first - the press. I started out using a Riley Hopkins Jr 4x4 press with joystick registration. It’s a press that is no longer made and I started to hate the joystick registration, but it was a great press to start my business with. I used that press from 2017-2022.
Thankfully I was able to upgrade way sooner than I had planned. I saw an add on instagram one day about a liquidation auction of a print shop and it caught my interest. I looked at the listing and there it was. A practically new Riley 300 8x6 manual press(https://ssp.ink/riley300). It was a dream press for me but I figured it would be a really long time before I upgraded. I mean, it’s an $8,000 press for goodness sakes. That was way out of my budget. Well, I logged on for auction day and ended up snagging the press for under $1,000! Incredible!
So that’s what I’m printing on today and I plan to print on it for a long, long time. I do plan to get a new press in the future but that’s only because I’m secretly aware of something that’s in-the-works and I know it’s going to be something I want. Stay tuned, that’ll be an exciting day if I’m able to make that upgrade.
Curing
To cure my prints, I only have a small 16x16 Riley flash dryer(https://ssp.ink/riley-flash). It’s not ideal, especially for water based inks, but I make it work. I’ve had it since day one and I’ve never had a single issue with it. Some day I’ll upgrade to a forced air flash and a conveyer dryer, but as long as I’m in the rental house I’m in, I’ll probably stick to my current flash.
Water based only
While we’re talking curing inks, I’ll go ahead and mention that I print with only water based inks. After working at a screen print shop that used only plastisol, I knew when I started my own business that I wanted to print with only water based inks. It was hard to learn, but I figured it out and I’m so glad I did. I’ll never make the switch. 100% team water based forever over here.
Washout booth
One of the first big purchases I made after my first full year was a 48” Sgreen washout booth. I decided to get it before a dryer or better exposure unit. Being in a rental and in a neighborhood, I wanted to be sure I was doing everything I could to keep things as clean as possible. A nice 4’ aluminum washout booth and an Sgreen filtration system are a must, in my opinion. You need these additions to your shop as soon as possible.
Water source and power
The companion to a washout booth is water and for me, that means running a house from the outside faucet, through a window, into the basement. It’s a pain, but again since I’m in a rental, I do what I need to do to make it work. I use a power washer for cleaning and washing screens and I highly recommend you do the same. Since I’m in the basement, I didn’t want something that’s too loud and I knew it needed to be electric. I opted for the Sunjoe SPX3000 and it’s been fantastic. It was cheap, so I don’t expect it to last much longer but that’s ok. It’s relatively quiet and has plenty of power.
Air compressor
Yes, you need an air compressor. Well I guess you don’t “need” it, but it sure is a nice thing to have around. After you wash a screen, often times the emulsion will have some residue and spraying it dry with the compressor is a great way to make sure the residue doesn’t run down into the stencil and harden. Again, I wanted something super quiet and I found the California Air Tools compressors and oh my word, these things are incredibly quiet. You can stand by it and have a normal conversation even when it’s running. I’ll never buy another brand, that’s for sure.
Film printer
For films, I have an Epson Artisan 1430 and I love it. It’s not a cheap printer if you get it new (around $2,000+) but I was able to grab one on eBay for $400. Before this I was using a standard Epson Workforce printer and I always had trouble burning screens because my ink wasn’t dark enough on the films. Plus, I was limited in the size of artwork I could do (8.5”x11” or smaller). But since upgrading two years ago to the Artisan 1430 I’ve had way better results in exposing screens. I also purchased the Blackmax ink kit which allowed me to swap all the color ink cartridges with new, refillable black ink cartridges. I highly recommend getting this kit because the ink is really opaque and will make your films a lot better.
Exposure unit
The exposure unit I have is an RXP tabletop exposure unit. It does not have the yellow working lights, it doesn’t have a vacuum top, and it’s not very big. However, it works great for me. I expose my screens for about 25-30 seconds using Baselayr Complete emulsion and it works great. I would like to upgrade to a vacuum exposure unit some day, but for now this one is working just fine.
Furniture
And last thing I wanted to mention was my furniture. I got it all from Sam’s Club and it’s really great quality. The brand is Seville Classics and I highly recommend them if you’re in the market for new shop furniture. They’re actually garage furniture, but works great for any shop. You can see the whole lineup available at Sam’s Club here: Seville Classics.
Shop tour
That about covers the main items in my shop. You can see all of these items in my 2023 shop tour below.
Free assessment